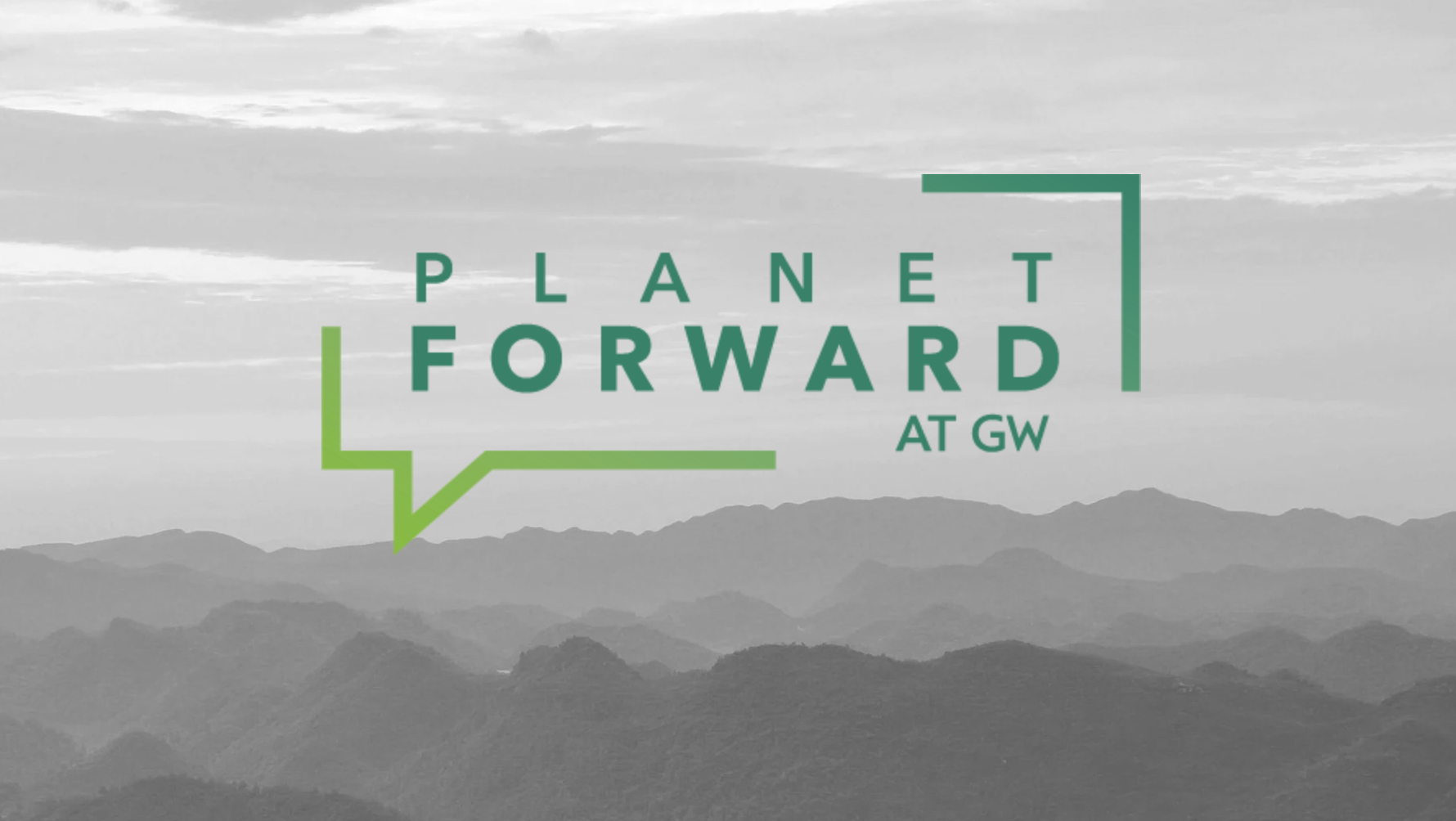
Advanced Composite Corrugated Core Panels: A Building Block of the Future
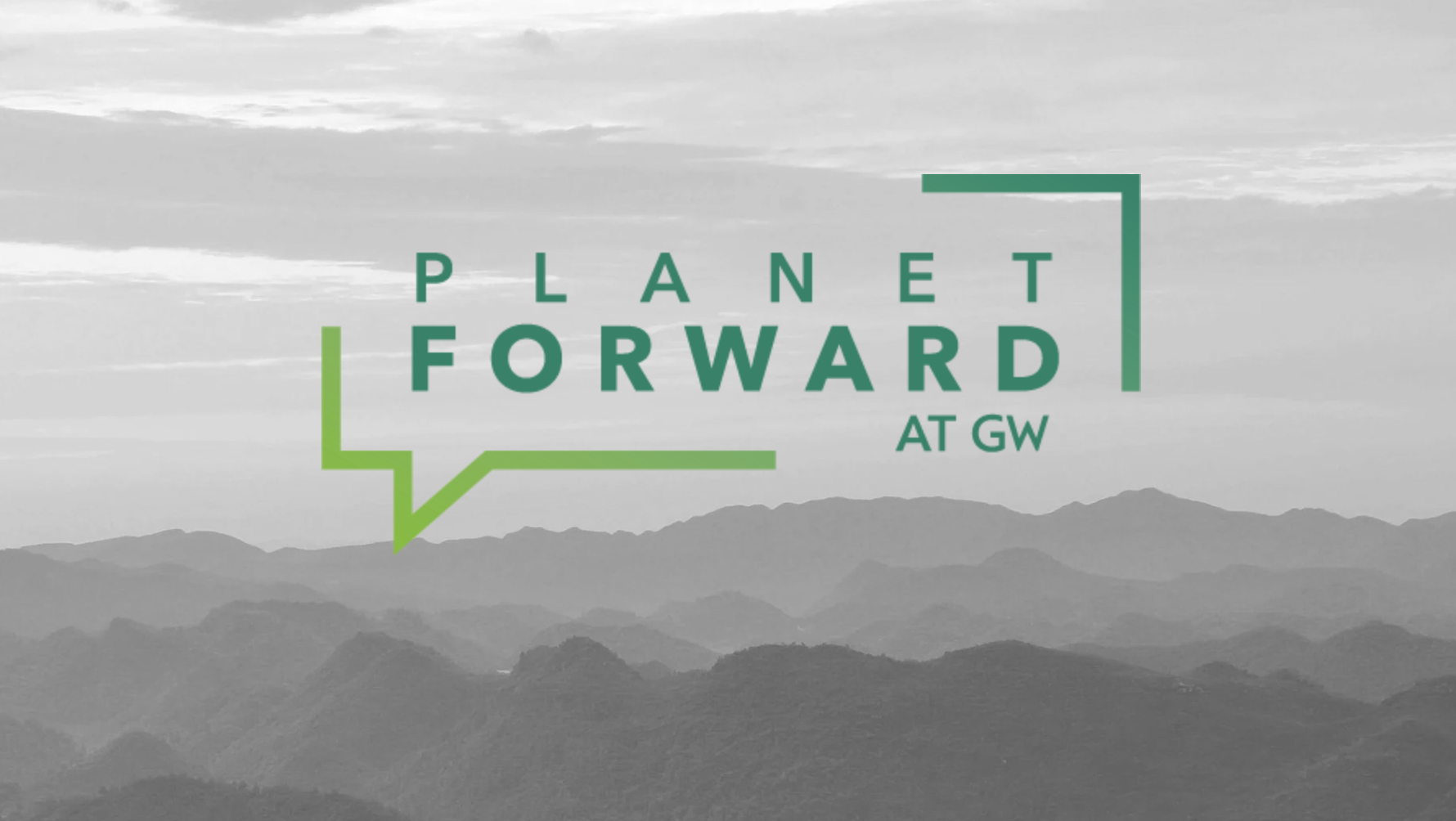
Abstract:
This document introduces a new generation of carbon fiber, Kevlar, fiberglass and other fibrous composite-based structural panels. The production method proposed is suitable for adapting current manufacturing processes used by the established and economically depressed wood products plywood/veneer industry. This process takes advantage of the industry’s current facility, management, labor, tooling, and capacity. It contributes to the re-invention of the wood products industry by addressing the changing needs of the 21st century with a set of product lines that complement existing veneer production methods. It results in a new core technology that can remain viable during economic cycles adversely affecting those of wood products.
Wood And Composite Panel Production Similarities:
There are numerous characteristics that are common to plywood/veneer panel manufacture and composite fiber panel production. Both manufacturing processes use panel sized ovens, 4-post compression presses, resins and resin-application machinery. The manufacturing facilities share similar and complementary materials handling sizes, scale of operational processes, production line flow and layout. Manufactured goods use the same styles of transport and distribution network. There are complimentary organizational and management skill sets from production facility to client base. Both distributors and retailers can use the same methods and scale of product warehousing, labeling, inventory control and tracking, transport and marketing.
This style of composite panel facilitates the transition of carbon and other fibrous structural materials to service a vast group of common commercial and industrial applications. The panel uses are complementary to those serviced by other more mature technologies. Wood, metal and plastic panels in their infancies were expensive to produce and were thus not common. Each of those materials developed to become industrial/commercial building blocks. The fibrous composite corrugated panel provides the aerospace, military, automotive and building industries with multi-purpose, reformable and standardized product lines that combine weight-reduction with impressive stiffness and stability. This new style of corrugated paneling may now be manufactured due to recently innovated and improved material and manufacturing efficiencies. Corrugation results in vastly less material use and decreased weight than current solid walled panels, such as those used in wind turbine blades. They provide a lighter composite panel while maximizing stiffness with a more durable panel than the common honeycomb core styles used in aviation. The panels are made from natural, well-known plastic or glass fibers which are held together with standard resin-like plastics. By example, most carbon fiber is made by heat-treating and carbonizing common Rayon fiber.
High-performance, commercial-grade, corrugated cores made from appropriate fibers are mated to a wide variety of surfaces including wood veneer, metal, common plastics or rigid advanced fiber composite cloth. The increased adhesive surface area strengthens bonding and overall stability when compared to honeycomb core panels. The panels provide an ideal combination of stiffness, toughness, impact resistance, weight-reduction, and usefulness for numerous flat and curved panel applications. This style of structural core succeeds by improving performance outcome while providing the visual surface aesthetic that is appropriate for each specific style of application.
Green Industry Impact:
Corrugated-core structural panels are a green technology facilitator. Specifically, these panels are designed to contribute to commercial and industrial technologies that require light, efficient, environmentally stabilized, durable and long-lasting parts. Current and future industries will succeed by offering excellent product quality with decreased environmental impact. Green benefits include:
Products require less energy to overcome inertia (to begin to move). Thus there is energy and fuel savings when moving payloads. While critical to meeting the requirements of electric and other lightweight motor vehicles, this applies to all land-bound and airborne transportation, both commercial and military. This is true regardless of power source and use.
Products require less input and expenditure of energy to achieve the maximum outcome. This is applicable to lighter moving parts for wind turbine power generation and ocean wave energy collection. Machinery that overcomes inertia and attains maximum output at lower minimum rates of movement results in greater net energy gain.
Carbon and other fibrous corrugated panels may be produced with various environmentally sound, biodegradable and recycled plastics.
Practical applications:
Power Generation:
Wind turbine propellers
Wind turbine towers
Offshore wave energy collection buoy housing
Architecture:
Cooling towers, Storage tanks/cylinders
Platforms
Deck Supports
Select framing
Stair Structures
Walkways
Structural beams
Floor decking
Roof decking
Transportation; aerospace, military and consumer:
Door panels
Floor panels
Siding panels
Vehicle chassis and other basic structural sleds
Sporting and other consumer goods
Why now?
Economic, energy and environmental realities dictate that manufacturing businesses continue to transition to lighter, stable and more durable goods that maximize physical characteristics. The recognized qualities of advanced fiber composite materials have not yet begun to service a broad range of common needs.
Advantages include:
In line with the current strategy of supporting industries that promote
green technologies, high tech manufacturing and family wages.
Develops a ‘new Core’ growth Industry for the United States.
Revitalizes an existing and historically dominant industry that has excess capacity.
Offers a new product category that services existing commercial needs.
Facilitates development of numerous spin-off and new product categories of industrial and consumer finished goods manufacturing.
Adds a multi-regional industrial scale product base that is complimentary with wood products manufacturing. This is due to the ‘designed’ co-usage of existing plywood facilities, machinery, tooling and manpower.
Provides a wide set of products with broad expansion capability, and which are not dependent on home and commercial building cycles. Thus it offers economic diversification and greater stability.
Services major, existing, well-developed and emerging markets within and beyond the United States, including aerospace, military, aviation and wind energy.
Stephen Bryant Mosher is president and CEO of Moses, Inc. Moses, Inc. is a small Oregon-based high tech company with a successful track record in the development of structural beams and other products for the music industry.